Gulf Tech Conveyor System
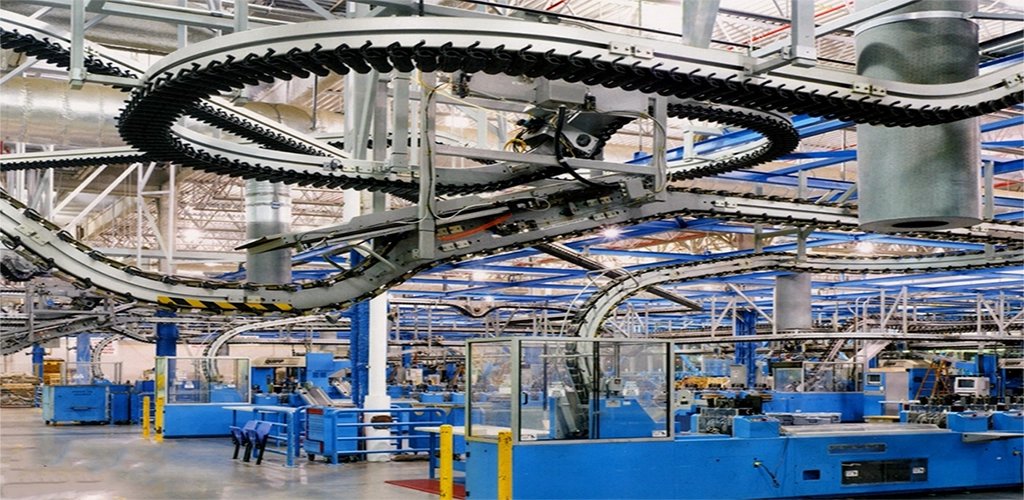
What is a Gulf Tech conveyor system? A conveyor system is a network of conveyors that move products from one operation to the next as efficiently as possible. There are many different types of conveyors, each of which accomplishes a different task. Warehouse managers incorporate multiple types of conveyors to ensure that their operations flow as efficiently as possible.
Benefits of a Conveyor System
Effective use of conveyor systems results in several benefits for a warehouse, including:
- Reduced walking time: Approximately 70% of warehouse worker’s time is spent walking. This time can be drastically reduced if conveyors are used.
- High speed sortation: Conveyors sort products at very high speeds. What would take a human several hours to accomplish, a conveyor can complete in minutes.
- Reducing picking time: Manually searching for specific items wastes valuable time. Conveyors interact with scanners to route and sort them effectively, reducing the time it takes to pick them individually.
It’s important to note that each conveyor’s benefits require use of the right conveyor. As each has its own function in a warehouse, you’ll need to know the proper use of each. Here are eight types of conveyors and their use in a facility.
8 Types Conveyor System
For a warehouse to operate at peak efficiency, it needs to optimize its transportation of products. While manual picking is an option, it wastes valuable time and leaves room for human error. Conveyors are a response to this problem that result in increased productivity and efficiency. Here’s an overview of a conveyor system in a warehouse and seven different types of conveyors that can be used to optimize the facility’s efficiencies.
1. Gravity Conveyors
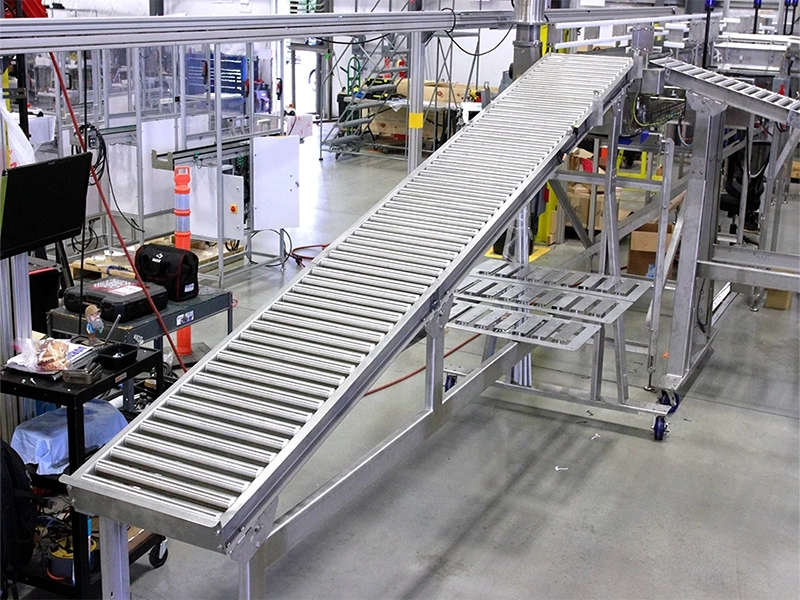
Gravity conveyors are a series of roller or skate wheel conveyors, but no motor. Instead, they transport the product using the weight of the product to move down an incline. The conveyor may also be horizontal, but the product must be propelled manually in these instances. These conveyors are best for heavier objects with flat surfaces and are typically used in pick modules or end-of-line interactions.
2. Belt Conveyors
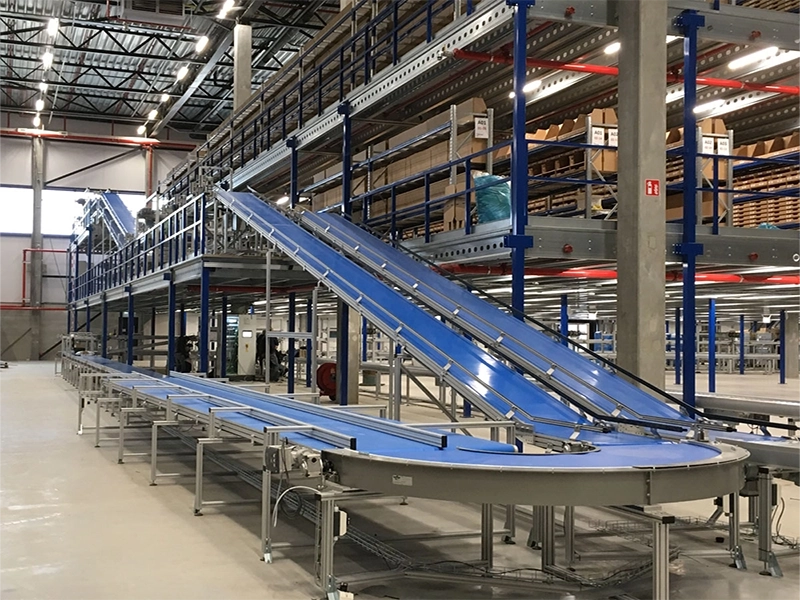
If you’ve seen airport workers loading suitcases onto a plane, you’ve witnessed a belt conveyor at work. Belt conveyors are what many people think of when talking about conveyors, mostly because they are widely used in public facing operations. They’re driven by a motor that operates two pulleys enclosed with a continuous loop belt and are often used to transport items up or down. Their traction works well with corrugate, so they can move cases through a change in elevation without a fear of sliding.
3. Motorized Driven Roller (MDR) Conveyors
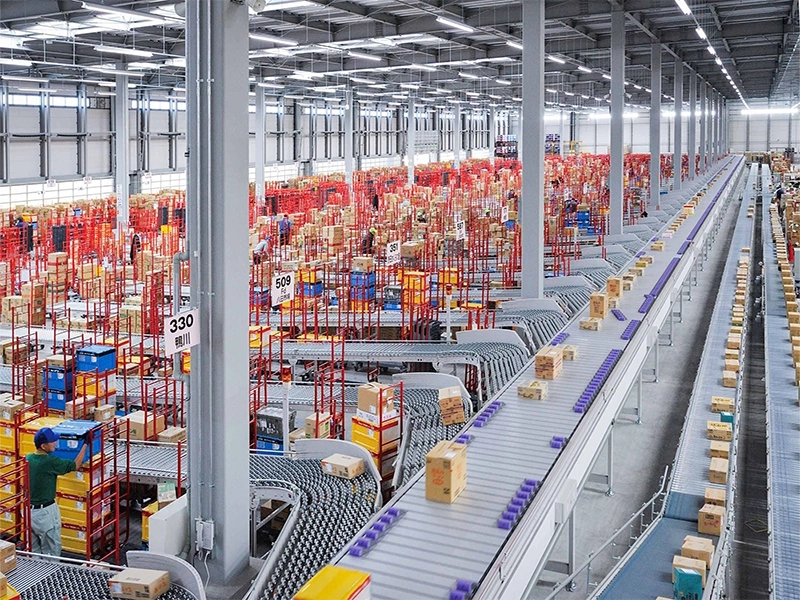
Traditional conveyor systems are driven by motors and gearboxes that control the entire conveying surface. MDR conveyors, however, are powered by individual motors enclosed within the rollers themselves. They typically consist of “zones” of rollers, in which one motor per-zone drives the surrounding carrying rollers. This configuration is quieter and safer than traditional conveyor systems. It can also run-on demand, reducing energy consumption and increasing power savings. It’s an excellent option for merging, sortation, and zone routing transfers within pick modules.
4. Sortation Conveyors
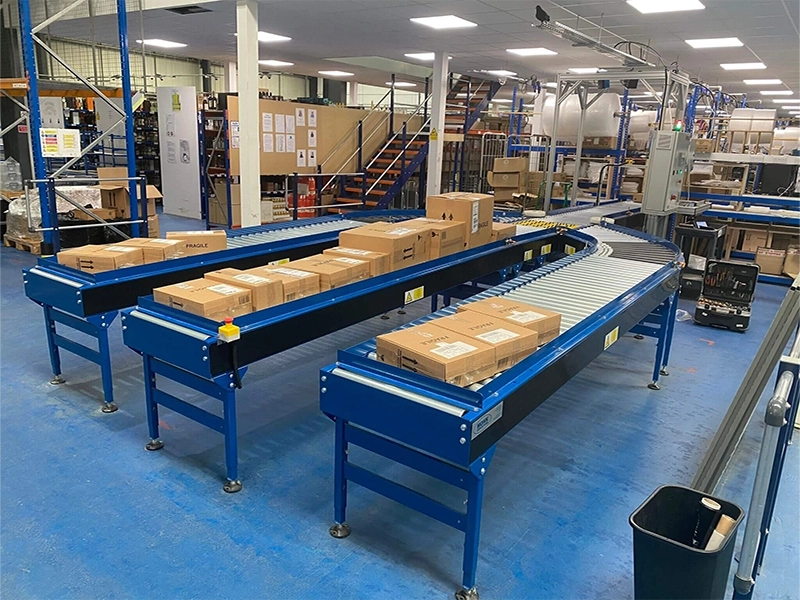
Sortation involves identifying items on a conveyor system and diverting them to their proper locations. There are many types of sortation conveyors that can accomplish this task through an interaction with software to scan items and redirect them to their correct locations. Some examples of sortation conveyors include:
- Pop-up wheel sorters: A conveyor with rollers that pop up underneath the case to move it at a 30 or 90 degree divert off the existing conveyor.
- Shoe sorters: Sortation conveyors that use sliding shoes to sort product off a conveyor at speeds of up to 650 feet per minute without damaging the product.
- Cross belt conveyors: These allow you to sort pieces or cases at thousands of units per hour. Each individual carrying surface runs in a loop and has its own divert mechanism and motor. These are excellent if you need to sort a wide variety of products with multiple shapes and sizes.
5. Accumulation Conveyor
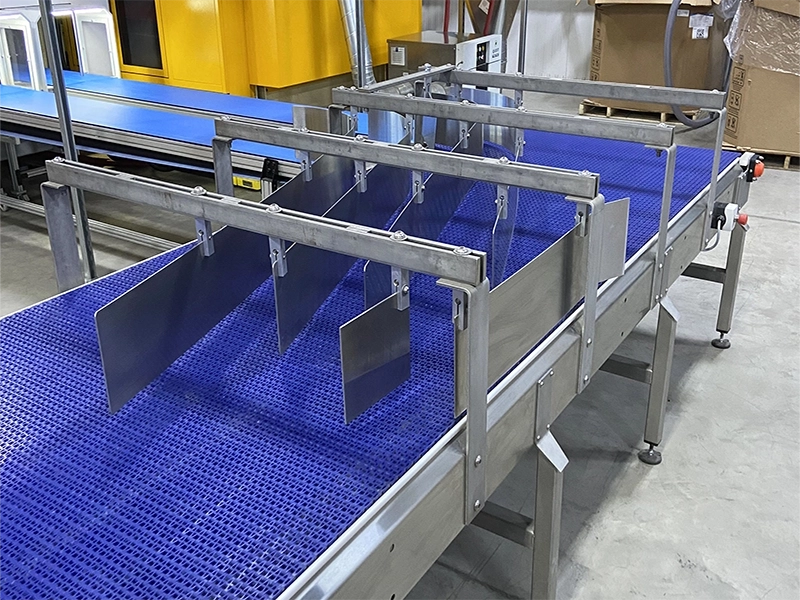
In a perfect world, picking would occur at the same rate as shipping. However, the reality is some buffer time is needed as one operation will flow quicker than the other. Accumulation conveyors are a response to this scenario. Whether they’re chain-driven, belt-driven, or non-contact 24v, they’re used to improve the throughput of order fulfillment operations by allowing cases to queue and be properly spaced between different zones or areas.
6. Overhead Trolley Conveyor System
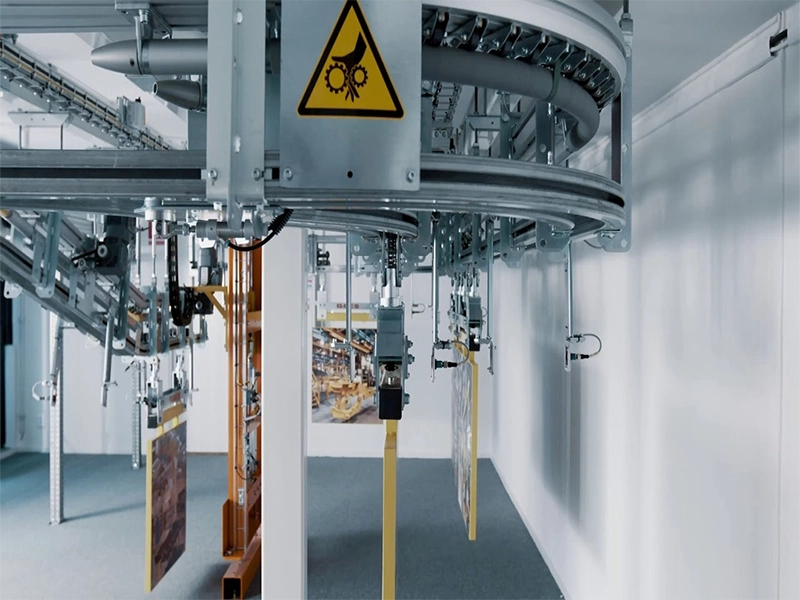
One area of a warehouse that’s often wasted is overhead vertical space. Overhead trolley conveyors optimize space by conveying and storing heavy items or hanging garments above heavy traffic areas. They can be used for a variety of functions including assembly line processes or empty corrugate accumulation and transportation.
7. Pick and Pass Conveyor
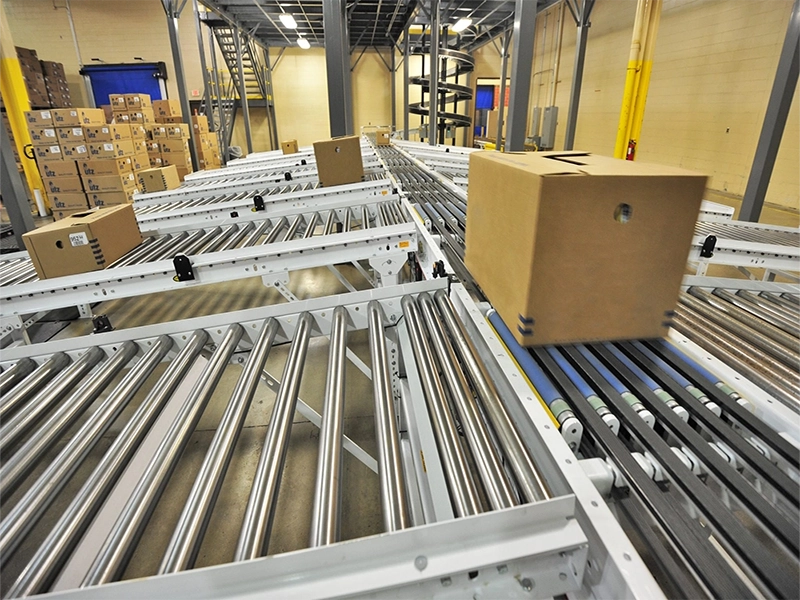
Pick and pass conveyors are used in pick modules that are long or multiple levels high. Also known as a zone routing conveyor system, these conveyors allow cartons or totes to be intelligently transported through a pick system to specific zones where the work is located. This reduces the number of totes queuing and immediately routes them to their next destination. This reduces workers’ travel time to collect containers for picking purposes, and increases their productivity. The alternative to intelligent routing for pick and pass operations is to have each carton or tote move sequentially through each zone, regardless of whether or not any activity is required. This can dramatically increase the amount of conveyor, labor and floor space required.
8. Empty Corrugate Conveyor (ECC) Systems
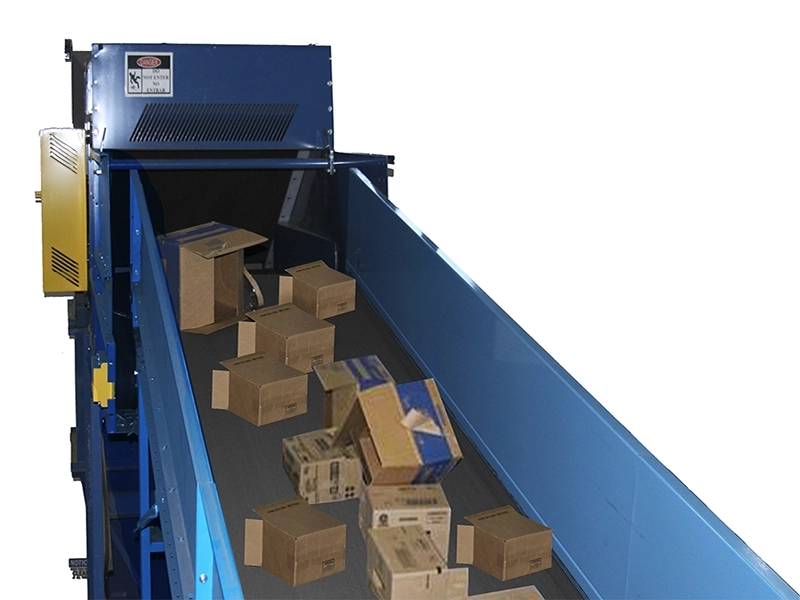
Also known as “trash conveyors,” these conveyors are designed to move empty corrugate from picking and/or packing locations to a specifically designated collection point. The purpose of this system is to reduce the amount of time spent on trash collection. This ensures that operators continue performing their primary functions instead of wasting time collecting trash. It also makes recycling easier and more economical by reducing waste. With ECC conveyors, items get transferred from a case into a tote or order carton from a piece picking environment. The empty corrugate is then thrown into the ECC conveyor which then goes to a compactor or a bailor for the company to recycle or resell.
Selecting the Right System for Your Facility
Unfortunately, there’s no universal conveyor that meets every operation’s needs. You must implement the systems that work best for your facility and its specific needs. Considerations include:
- What type of product do you need to move?
- How many cases per minute are you trying to move?
- How well do the conveyors work together?
- Can you access them?
- Can you maintain them?
- Is there a better solution?